Why are Utilities Rejecting Solar Farm Power?
Share this article:
With current Government and Municipal Mandates, Solar Farm DER (Distributed Energy Resource), connect to a specific POI (Point of Interconnection), on the electrical grid. The POI connections change at different capacity outputs and voltages. Where the POI connection is, the level of Voltage at which it connects, and how far a distance all matter. As a function of all of those factors, the quality of the DER-made power, at the Point of Interconnection may matter the most. The utility may reject the planned Solar DER, or worse, reject the power after the plan has been constructed. These are new challenges for the Solar Power Industry today. There are some answers.
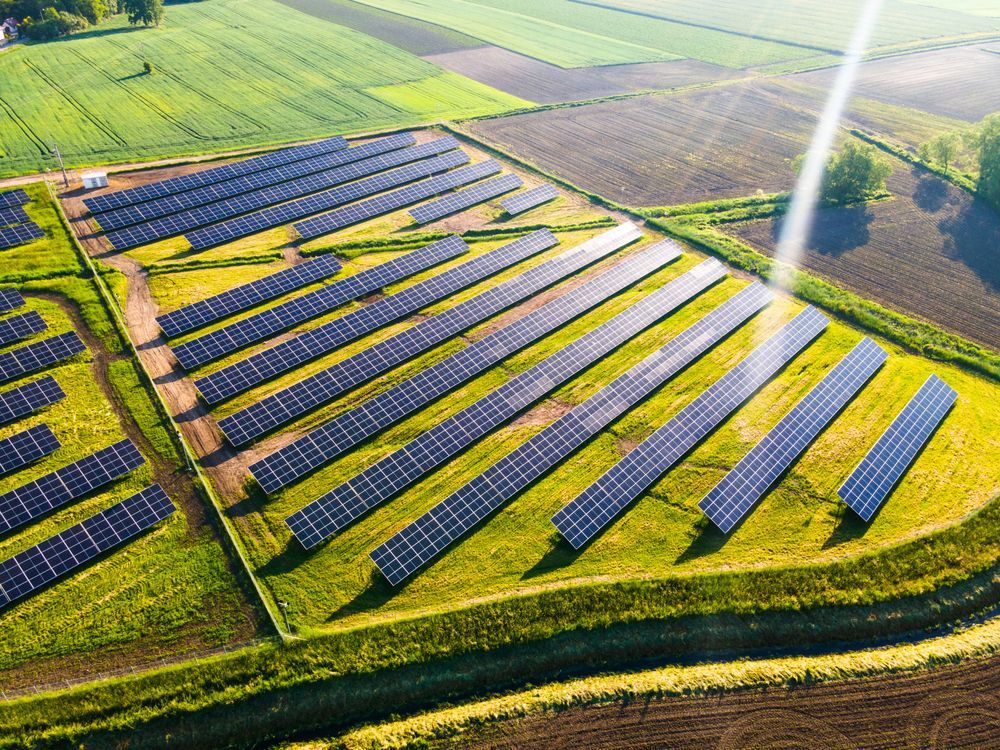
Utility Rejected Solar DER Interconnect Power at Point of Connection
The Electrical Utility, who is tasked with collecting and distributing all power generated by Solar DER’s, reserves the right to reject the power generated at the connection point POI. The Utility will maintain strict guidelines as to what voltage parameters, ampacities, resonances, and disturbances it will tolerate into the electrical utility grid system. It may review a plan for a specific DER in a location at a specific voltage, once testing is done, require the DER connect at a different point on the grid miles away and at a different voltage. This is costly to the project and its original expected payback.
Solar Projects Stopped in their Tracks by Reactive Voltage Control RVC
As a developing issue unrecognized largely by the industry,
Reactive Voltage Control RVC , and
Reactive Power Control RPC , are now straight in the crosshairs of the utility transmission administrators. Reactive voltage generated by Solar DER systems are an intently measured data point by the utility. Reactive Power is damaging to distribution systems, lowering real power capacity and efficiency. Reactive power will increase equipment replacement and maintenance costs to manage not only the utility transmission, but everything receiving the so-called contaminated energy.
What Amount of Solar Reactive Power will Utilities Accept?
Power Lines absorb and provide reactive power on a normal basis. Devices absorb reactive energy depending on the power factor. When a generative load starts in the factory it uses a percentage of reactive power and creates heat. The lower the power factor, the higher the reactive power consumption. Reactive Power does not travel well over electrical lines. Therefore, a requirement to collect more “real power” by the utility is a prudent policy. The Solar Industry, at this time is guessing what the utility will require for RVC Reactive Voltage Control long term. DER’s are relying on single case examples, and Plan Review’s by the utility to find out this feedback after design. Again, convoluting the project budgeting process.
Are There Solutions?
As the RVC and Reactive Power conversation is developing as a major trending topic for Solar Farm installations. There are ways to mange RVC and RPC. Current options to mitigate the reactive power issue area available depending on the size and scale of the operation and distribution requirements.
Review your RVC and RPC issues with Voltage Correction
We understand that finding the right solution for all industrial power issues is important for maintaining the operation of your business. At Voltage Correction, a Division of Facility Gateway Corporation, we pride ourselves on quality customer service, and overall industry experience in the mission critical electrical power solutions market. Our team members are available to assist you throughout the system selection process and will review the specifications and concerns you address. Voltage Correction
is a provider of power correction services globally. Please contact your Voltage Correction representative to discuss power correction options for your facility and plastics operation.
Connect with Us:
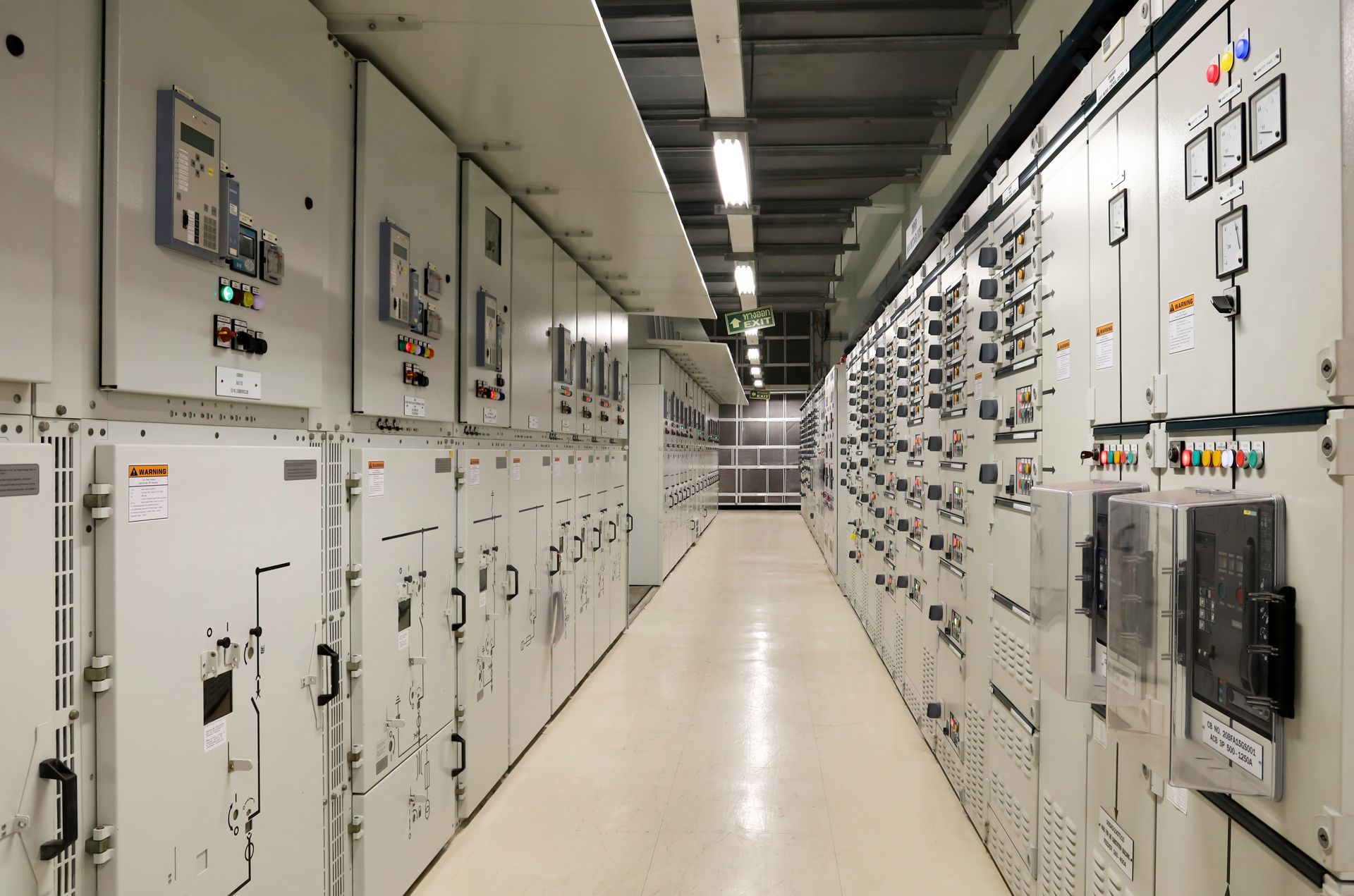
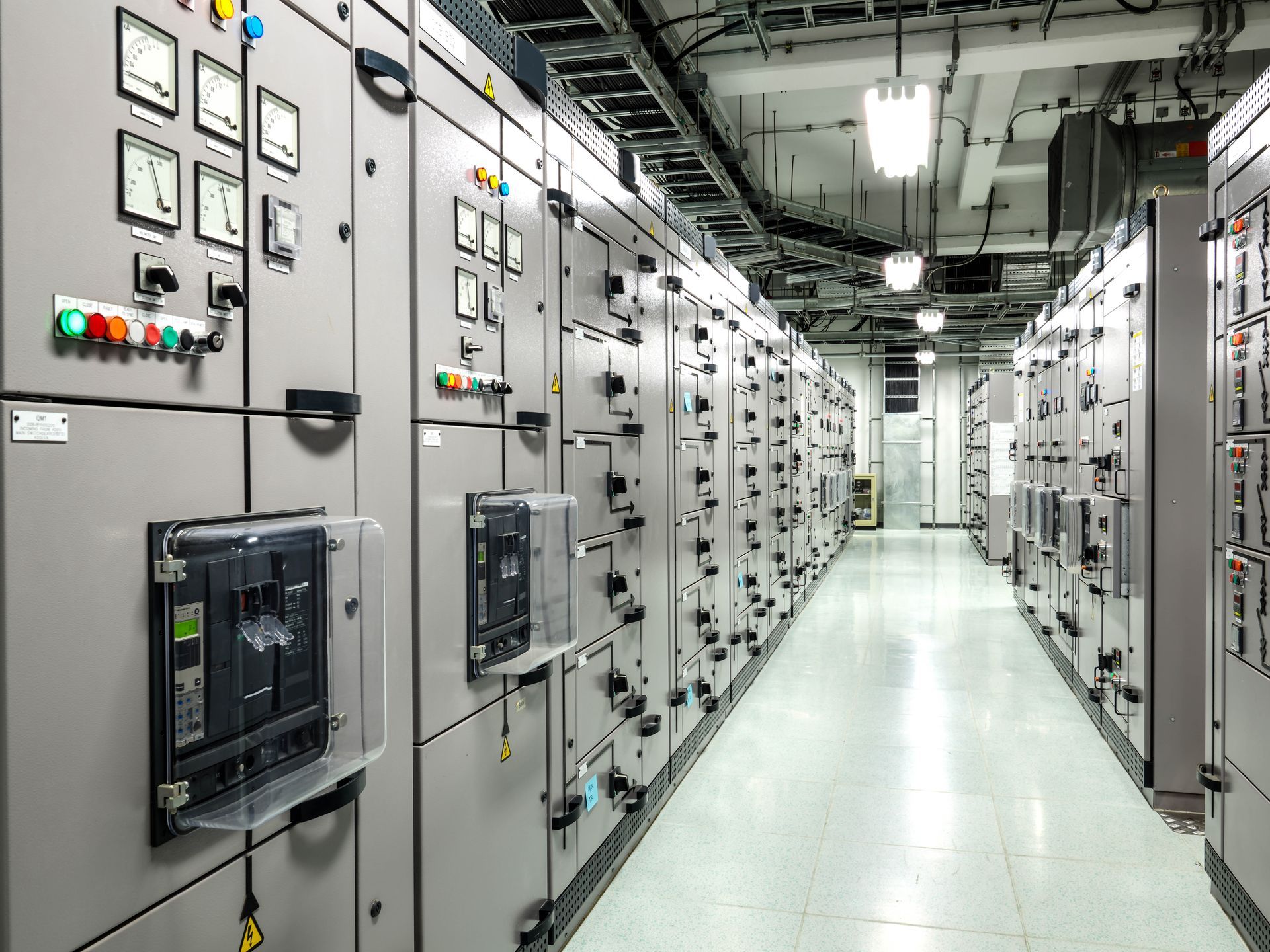
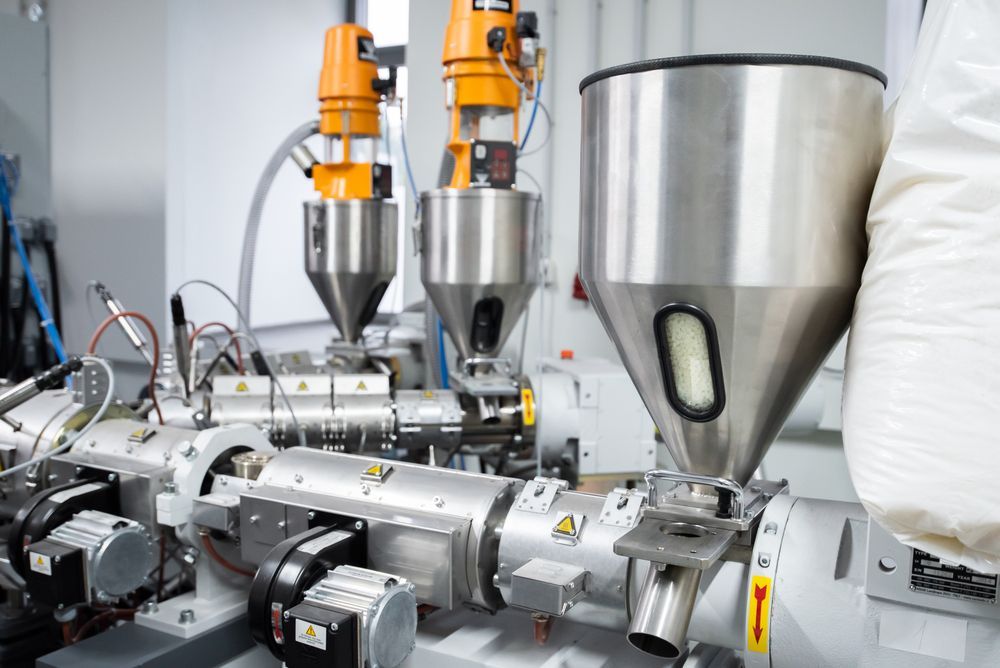