Voltage Sags Affecting Manufacturing Processes: What They Are and What to Do About Them
Share this article:
The most common event that affects power output and quality is a voltage sag. Does your industry rely on industrial equipment, including process controllers, PLCs, adjustable speed drives, and robots? Do you notice their heightened sensitivity to voltage sags? In the content below, we discuss voltage sags in terms of what they are, what to do about them, and how to prevent them from happening.
Voltage Sags: What Are They?
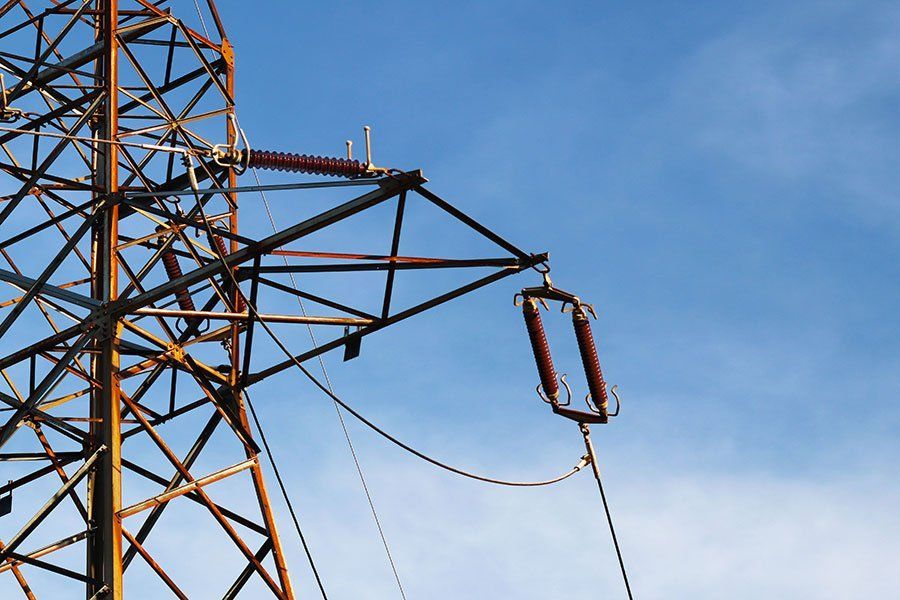
Also referred to as voltage dips, voltage sags are brief reductions in electrical voltage by at least 10%. As defined by the IEC 61000-4-30 standard, the voltage sag lasts for less than one minute yet longer than eight milliseconds. The magnitude of a sag ranges between 10% and 90% of the normal Root Mean Square (RMS) voltage at 60Gz.
As voltage sags are a common power quality event, they can occur up to several times annually, yet appear more frequently at equipment terminals. In recent years, it became required that electrical equipment be manufactured with the capability of riding through brief voltage sags. This
requirement of using IEEE 1668 for power quality varies on the sag characteristics and the equipment application.
Voltage Sag: What Causes Them?
Voltage sags are caused by abrupt increases in electrical loads such as short circuits, faults, motors starting, or electric heaters turning on. Alternatively, they can derive from abrupt increases in source impedance, typically caused by a loose connection.
Often, sags create a minimal disturbance among disturb incandescent or fluorescent lighting, motors, or heaters. However, some of your electronic equipment may lack the sufficient internal energy storage necessary to effectively ride through sags in the supply voltage. Your other equipment may be able to go unphased through very brief, deep sags, or it may be able to ride through longer, shallower sags.
Below, we explore the most common voltage drop causes.
Voltage Sag: What Causes Them?
Although most would suspect the local utility to be responsible for a voltage sag, it is often derived in the transmission of power between the utility distribution point and your electrical service. Taxed electrical grid, totality of different facility’s impact on the power supply, heat, and weather events can all contribute to creating sag activity. It is something the utility will not be able to control or affect. It is up to the consumer to correct the effects of sag activities.
Power quality problems can occur from either side of the electric meter. However, it is sometimes difficult to determine the source of voltage sags or other power quality problems.
Natural Events
Did you know that a voltage sag on the power grid can affect users in greater than a 100-mile radius from the causing event? Voltage drops that occur on the utility side of the power meter can either stem from natural events or human-created scenarios. Common human-created events are switching operations.
The most common natural events include:
- Lighting
- Wind
- Trees falling onto power lines
- Construction workers digging into buried cables
- Squirrels and rodents
- Equipment failures
- Traffic accidents
Voltage Sags recently occurring in the Northeast have been caused by excessive heat. An irregular weather pattern located over that part of the country has been a considerable tax on the electrical grid system.
Physical Results of Voltage Sag Activity
The chart below explores what physical results occur amid voltage sag activity.
- 10% +/- sag/surge: Continual wear on PLC’s, boards, line equipment, motors, lasers, and process equipment.
- 20% – drop in voltage: Considerable spike in amperage due to the low voltage. You may see long-term or immediate damage to equipment.
- 50% – drop in voltage: Will appear to be an outage, flicker, or drop of light output. There will be a considerable amperage spike to all loads that will result in damaged equipment.
- 80% drop in voltage: Power loss occurs and there may be a gradual sag if on one phase. Visibly damaging to all electronic equipment.
What Can You Do About Voltage Sags?
The most effective solution to voltage sags is determining if a piece of equipment is more sensitive to voltage dips and implementing Active Voltage Correction.
Identify Sensitive Equipment
To prevent any further damage or wear to your equipment, it is crucial to detect and isolate individual pieces of equipment that appear more sensitive to voltage sags. Doing so allows you to better determine where to deploy sag correction devices. Sag correction devices can be installed at various locations, including control panels, machine levels, bus levels, and even at the plant service entrance.
To best determine where to implement the correction devices, you must evaluate the percent of sensitive loads within the plant, ease of installation, downtime cost, solution cost, and return on investment. Additionally, if your plant works with a larger load, it will be necessary to install a three-phase solution.
Implement Active Voltage Correction
Voltage Correction provides voltage stability by correcting and holding the voltage to avoid deviations that slowly wear out your control and process equipment. This is accomplished by implementing either an Active Voltage Correction (AVC) , an Active Voltage Regulation (AVR) device or an Industrial UPS System.
By doing so, you can reduce time spent in recurring maintenance tasks involving the replacement of boards, capacitors, and other parts. Additionally, an AVC or AVR reduces your downtime spent to reset equipment and processes.
The following is what an AVC (Active Voltage Correction ) System can provide for sag activity:
10% +/- sag/surge: 10% +/- sag/surge regulation AVC corrects to nominal power voltage
20% – drop in voltage (Sag to 80%nv): AVC corrects to 100%, 3 phase for 3+ minutes, 1 phase Continuous
50% – drop in voltage (Sag to 50%nc): AVC corrects to 90% 3 phase for 1 minute, 1 phase 100% continuous
80% drop in voltage (Sag to 20%nv): AVC corrects 1 Phase 100% continuous
Voltage Sags: Correction and Maintenance with Voltage Correction
At Voltage Correction, our electrical engineering experts know which voltage regulation solutions will best maintain your industry and reduce the occurrence of voltage sags or swells. By analyzing your current power output and monitoring the electrical environments in your facility, we can capture nominal voltage, sags, surges, and events that would otherwise wear down your equipment.
Our Voltage Correction experts can complete a site survey, assess your facility, and install a power metering device. When you install equipment that corrects power and holds voltage within your facility, you will have the proper protection in place to defend against all outside influences of power. Halt the wear-and-tear on equipment in your facility by implementing a stable voltage and power factor.
Contact us today to learn more about our voltage sag correction and metering services or to schedule a site visit. Call 855-240-6776.
Connect with Us:
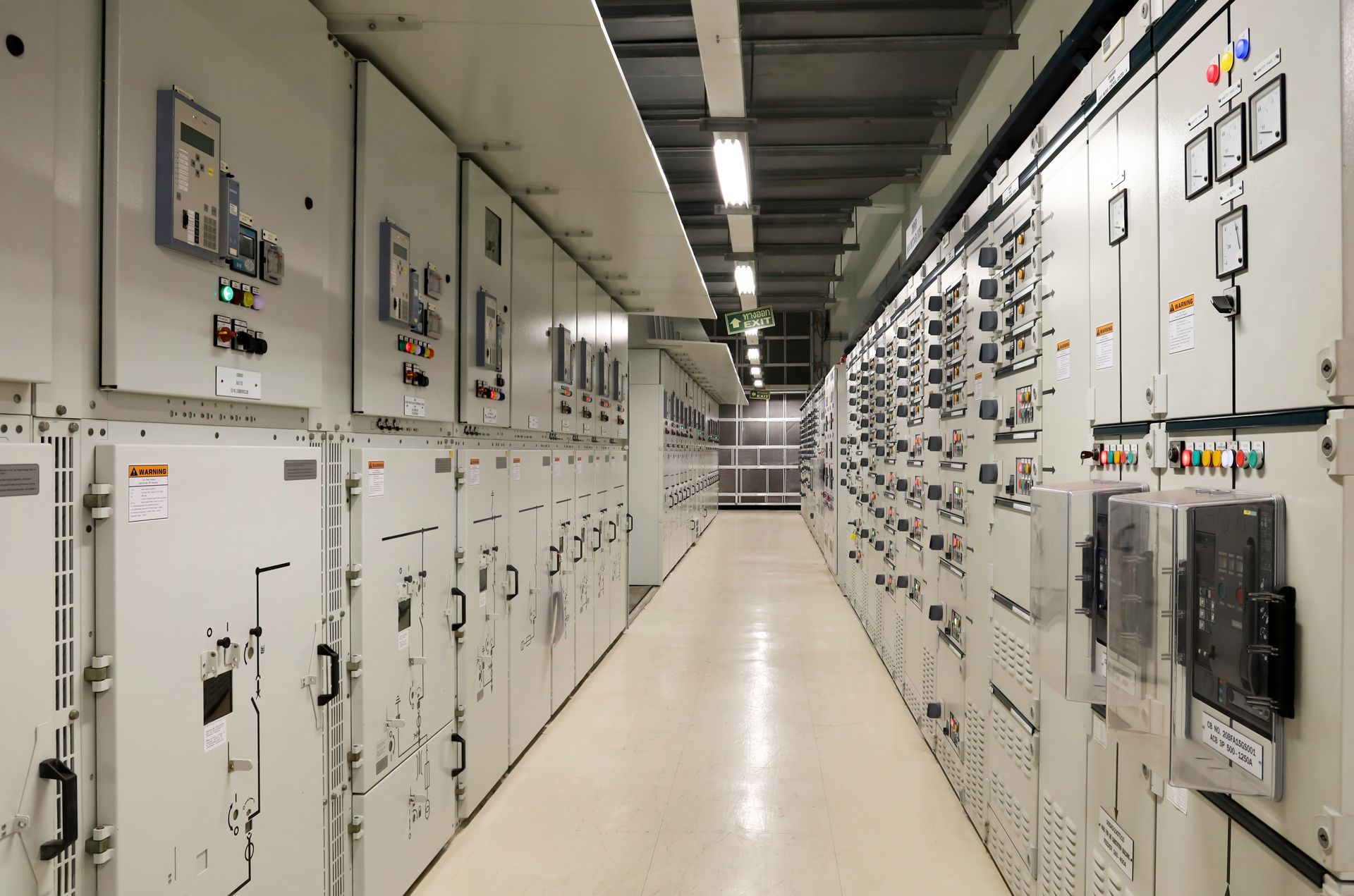
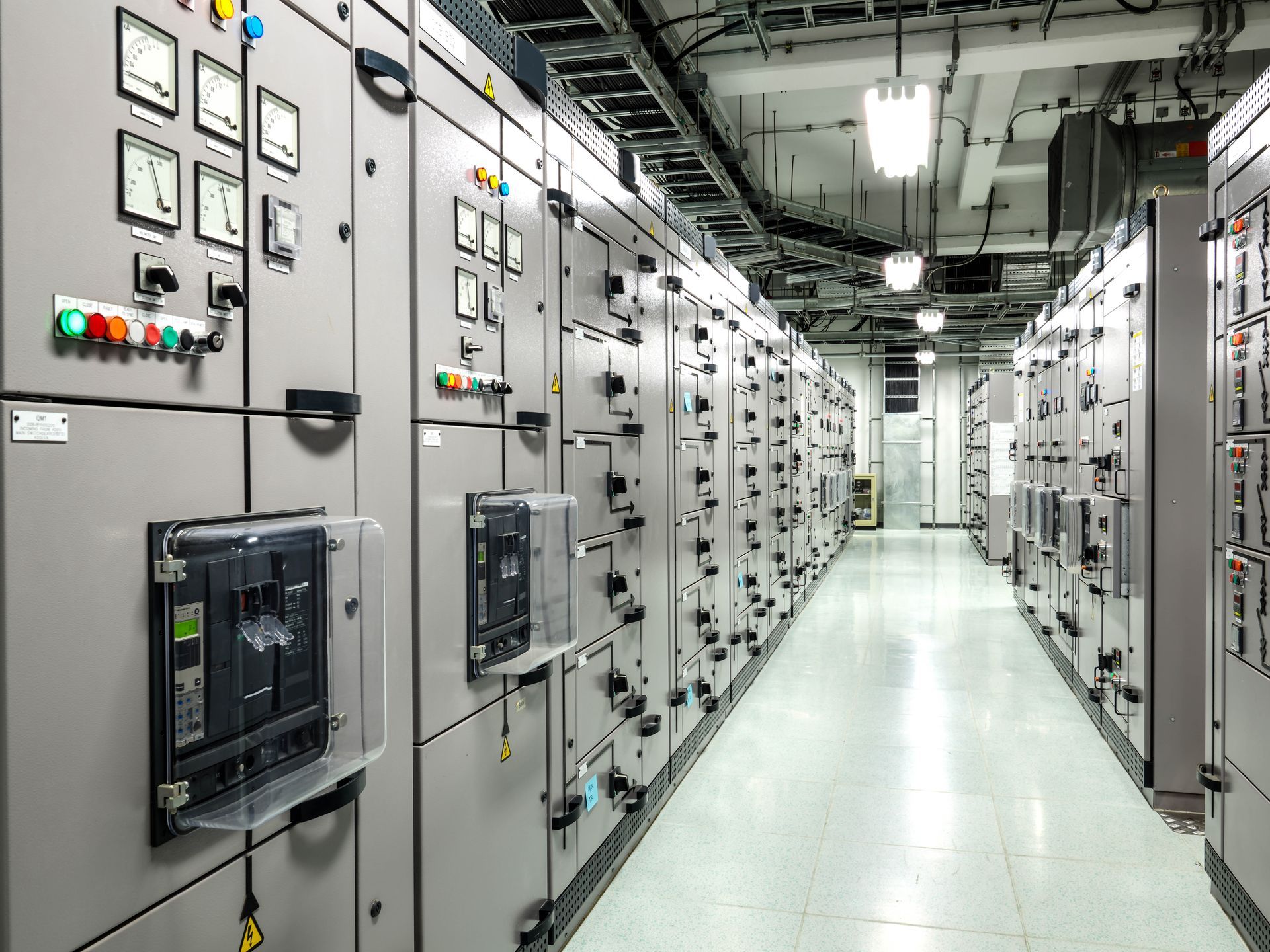
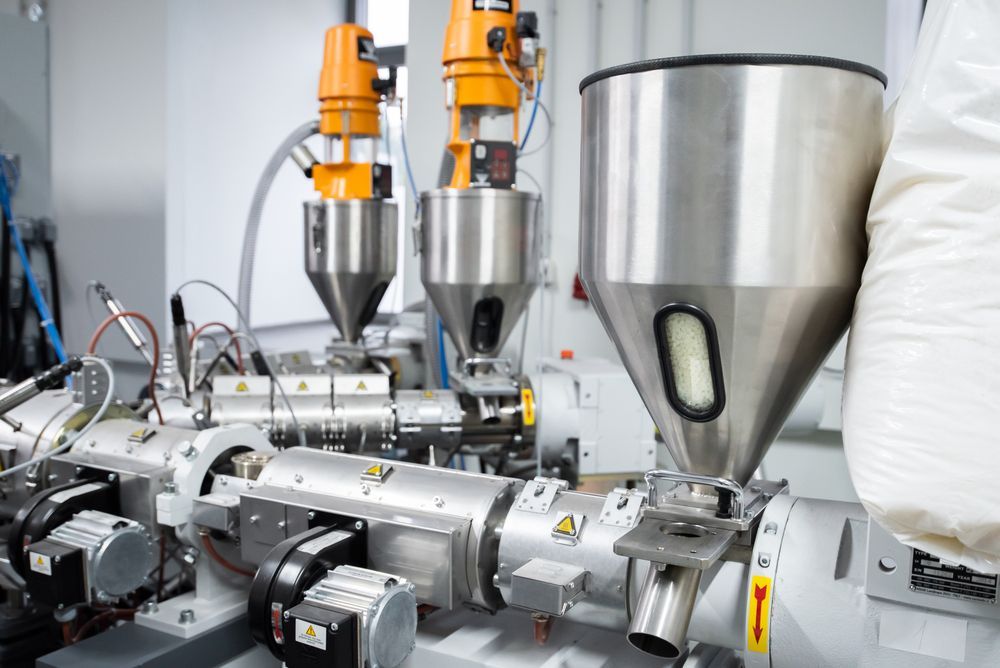