Transformer-Based vs Transformerless UPS for Industrial Applications
Share this article:
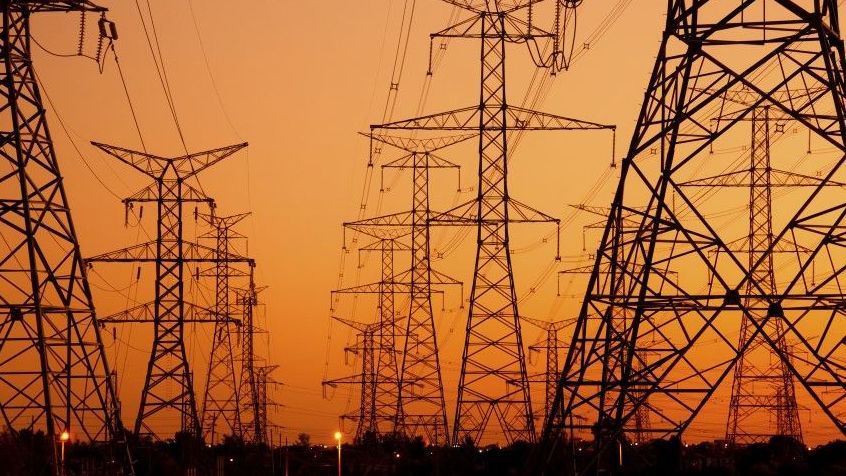
A transformer-based ups system provides an isolation mechanism. There are inrush currents from all the mechanical equipment. This is not the place for a traditional computer UPS system.
Why a Transformer-based UPS System?
Back in the 1970’s, 1980’s and 1990’s, most UPS systems all had transformers. One of today’s 3kVA UPS systems that sits next to your computer in your office would be 6’ wide and the size of a chest freezer. The componentry was larger, transformers were used on the input and output side of the UPS system.
The output of the UPS was controlled by transformer power. When the industry started converting to higher technology inverter systems. More recently the IGBT (Insulated Gate Bipolar Transistorized Inverter), things changed. Footprints got much smaller; energy efficiency went up. The weight of the system became much less.
Where do I Use a Transformer Based UPS System?
Enter a harsh environment such as a manufacturing plant, a plastic extruder, or 3d Printing facility. The loads are dynamic. There are inrush currents from all the mechanical equipment. This is not the place for a traditional computer UPS system. A transformer-based ups system provides an isolation mechanism for the incoming power against the inductive, or high tax loads on the output of the UPS.
Transformerless UPS Systems: Understanding the Limitations in Industrial Environments
Transformerless UPS systems have become more common in commercial settings, primarily because of their compact size and energy efficiency. However, in the context of industrial applications, these systems often fall short of the protection and performance needed to maintain stable power under heavy load conditions.
Why Transformerless UPS Systems Are Often Less Effective in Industrial Environments
Industrial facilities face unique power challenges, including high inrush currents and frequent power surges, which transformerless systems are not built to handle effectively. Here’s how transformerless UPS systems compare to transformer-based UPS systems:
- Surge Protection and Isolation: Unlike transformer-based systems, transformerless UPS systems do not offer the same level of isolation from electrical noise and surges. In an industrial setting where machines generate significant power fluctuations, this leaves equipment more exposed to potential damage.
- Handling Inrush Currents: Many industrial machines, such as plastic extruders and manufacturing equipment, require significant inrush currents at start-up. Transformerless UPS systems struggle to manage these high currents, while transformer-based systems are specifically designed to protect sensitive equipment in such environments.
- Space Efficiency vs. Durability: While transformerless UPS systems are smaller and may save space, they lack the robust build needed to endure the harsh conditions of industrial operations. Transformer-based systems, with their stronger construction, are far more reliable in dynamic industrial settings.
Importance of Understanding Transformerless UPS Systems
Even though transformerless UPS systems are generally less effective in industrial environments, understanding their operation helps illustrate why transformer-based systems remain the gold standard for industrial applications. Transformerless UPS systems may have a role in facilities with lighter, more stable loads, but for complex industrial demands, transformer-based systems provide the necessary protection.
Transformer Based UPS Systems for Industrial Applications
A traditional UPS system that originally was design for data centers will perform well to support those computer processes intricate to the manufacturing process. It will not do a good job supporting the mechanical and physical process type loads, or high inrush loads such as cooling systems. There will be a combination of systems to properly support all the loads deemed critical in the facility.
Today’s Industrial UPS System
Today’s industrial ups looks much like the older transformer-based ups system of the 1980’s and 1990’s. However more modern componentry, inverter systems, as well as the transformer provide for a robust system. These products can withstand he dynamic load environments such as a manufacturing process facility. They can backup runtime via flywheel systems, ultra-capacitors, and a variety of battery systems.
Choosing the Right UPS System for Your Industrial Facility
When selecting a UPS system, it’s crucial to consider your facility’s specific power needs:
- Transformer-Based UPS Systems are essential for environments with high inrush currents, dynamic mechanical loads, and frequent power disturbances. These systems are built for industries like manufacturing, where protecting equipment from voltage dips, surges, and electrical noise is paramount.
- Transformerless UPS Systems may be considered in smaller industrial environments with more predictable power conditions and lighter loads. However, they are often less effective in heavy-duty applications and do not offer the same long-term protection that transformer-based systems provide.
At Voltage Correction, we can help guide you through the decision-making process and determine which system best fits your industrial application’s needs. Contact our technical representatives today for assistance.
Which Transformer-based UPS do I choose?
Ferrrups Ferroresonant UPS System 500VA-18kVA
One of the first widely used transformer-based UPS systems was the Ferrups Ferroresonant UPS system by Best Power. This UPS System is still being made and used today. Eaton now owns the Ferroresonant line of Ferrups UPS Systems. It is now called the FX Series Ferrups UPS. It is built from 500VA to 18kVA. It is widely used on manufacturing environments. It can withstand hot environments. It is a bulletproof protector of loads in harsh environments.
3-Phase Large Transformer-based UPS Systems 100kVA – 3000kVA
Your Power Quality Specialist at Voltage Correction can provide you a quote for a Transformer based UPS System. For inquiries on Transformer-based UPS systems contact Voltage Correction today for a consultation on how we can help you protect your equipment and business from damaging voltage fluctuations.
Or Call 855-240-6776.
Have a site survey done to survey your facility and install a power metering device.
When you install equipment that will correct power and hold voltage within your facility, you will be providing your facility with protection against all outside influences of power. Halting wear and tear on other equipment in the facility by having stable voltage and power factor is the goal. The long term positives are lowered operations and maintenance costs by limiting voltage and amperage anomalies inside the facility. It is common to vet these issues by installing a monitoring device at the service entrance of the facility utility power. This is a low-cost method to really understand these issues and to make a proper diagnosis.
We are available to review electrical one-lines, Power Reports, Demand Usage, and any other data on your facility power.
Call your Voltage Correction Technical Representative today to discuss options to increase efficiency in your facility and correct our facility power issues!
Connect with Us:
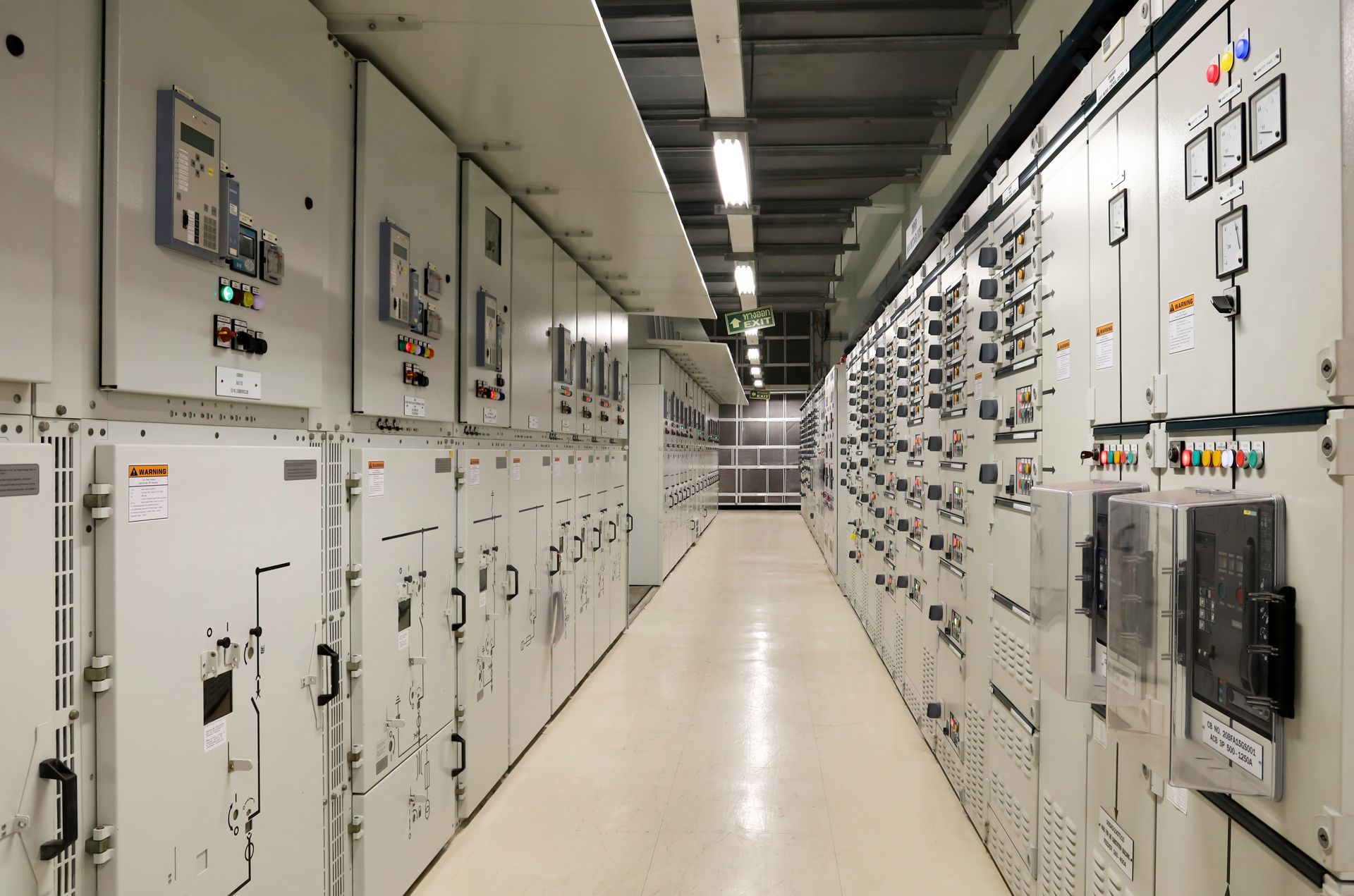
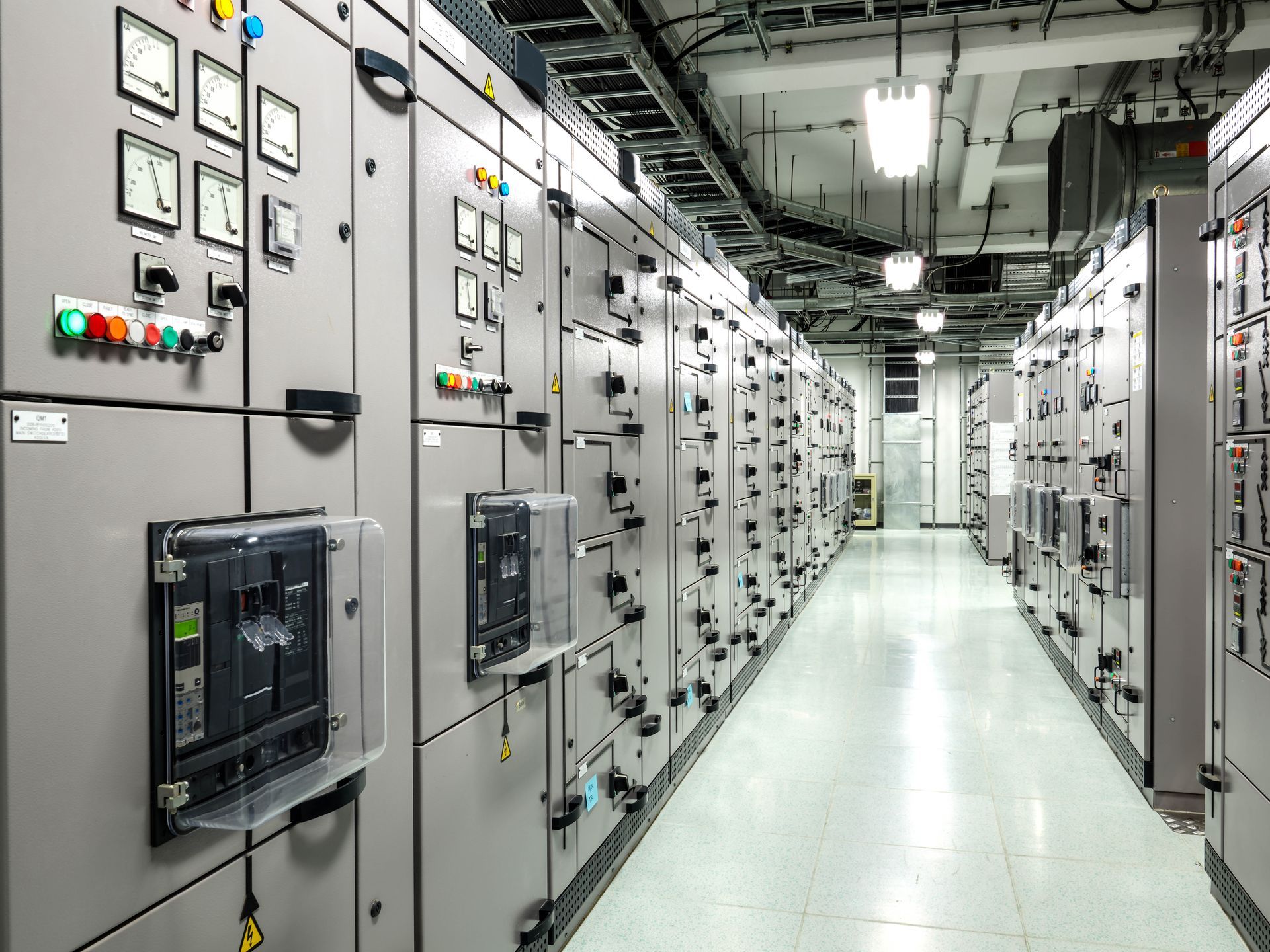
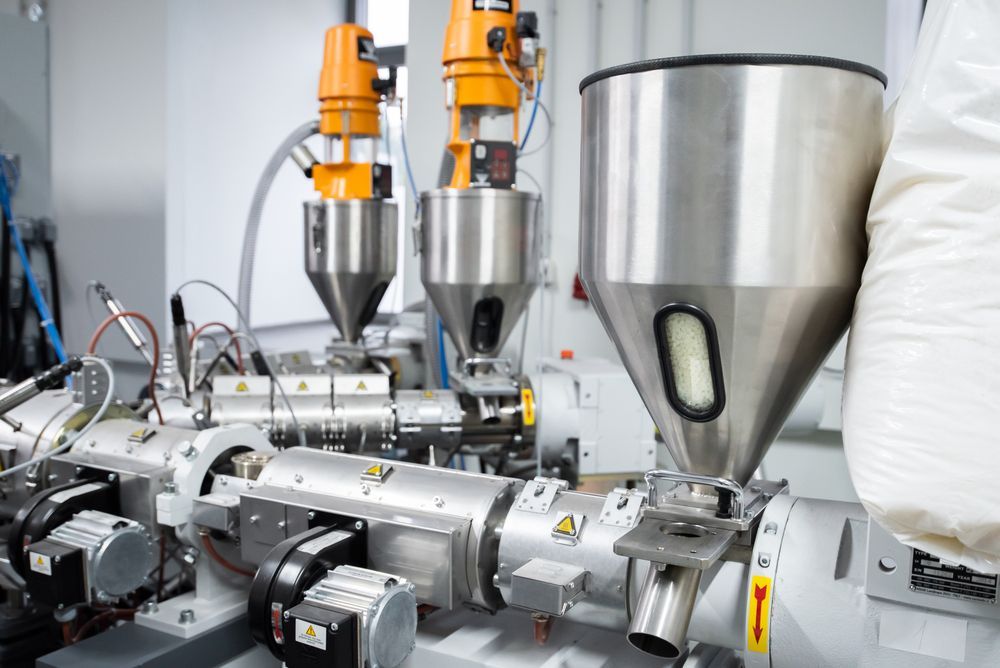