Power Outages are Increasing Across the Nation – Here’s How to Protect Your Facility’s Supply
Share this article:
According to Popular Science , the United States experiences more power outages than any other developed country. Due to a severely outdated power grid, (the oldest American power line date backs to the 1880s) the ever-increasing demand for power is pushing our system to the absolute limit.
Climate Central , an independent nonprofit scientific news source, found that major power outages affecting more than 50,000 homes or businesses became ten times more common from the mid-1980’s to 2012. On average, these outages cost $18 to $33 billion per year for businesses in lost wages, spoiled inventory, missed business opportunities, and more.
So how can we increase our power outage prevention protocols in order to protect ourselves and our businesses? In this article, we will take a look at a few of the most common causes behind the influx of power outages, and how you can manage your power supply with the latest technology to ensure a healthy and uninterrupted stream of power.
What is Causing These Increased Power Outages?
Currently, there are two main causes behind the onset of increased power outages: increased inclement weather and an aging power grid. A report conducted by the US Department of Energy found increased weather events across the nation to be the leading cause of power outages in the United States. As the weather continues to worsen, we can expect our aging infrastructure to be continually battered, which will in turn lead to even further, and more rampant outages.
Additionally, the weak infrastructure associated with our power supply is extremely vulnerable to cyber-attack. Many sources suggest that one well-timed and well-executed attack on our power supply could cause widespread damage for many users.
What is the Best Solution for Preventing Outages at My Facility?
Initially, it would appear as though upgrading our power supply infrastructure would be the best course of option. Not only would an updated power grid provide better protection from weather and cyber-attacks, but it would also help boost power outage prevention by making the entire grid significantly more efficient. Unfortunately, such updates are estimated to cost more than 4.5 trillion dollars for the United States. That large price tag has discouraged efforts to replace equipment and both industry leaders and the US Government are unlikely to change their stance on this issue any time soon.
For business leaders, the smartest solution is to invest in onsite power outage prevention solutions of their own. Fortunately, with onsite power generation costing less than utility for the first time in US history, there has perhaps never been a better time for such a transition. Below, we will take a look at a few of the most effective and efficient methods of power outage prevention.
Power Outage Prevention Methods
Short Term Power Outages
Frequently, people mistake short term power sags as a power outage. While the lights may flicker and your power supply may be temporarily interrupted, these sags are much easier to correct than long term outages. Fortunately, 90% of industry power problems are due to sags that were either internally derived or externally created.
The best way to combat these types of outages is to install some form of voltage regulation or protection. Active Voltage Correction (AVC) can be achieved in several different ways for short term utility outages.
Active Voltage Correction with Ultracapacitors
As the most expensive solution, ultracapacitors are capable of providing long term static solutions with little attention or maintenance required. Those high up-front expenses will quickly pay off with a low, annual maintenance for 15-20 years. With a reliable run time, ultracapacitors store energy in the form of static charge, as opposed to the electrochemical reactions of batteries.
Other benefits of ultracapacitors include their high-power density, nearly instantaneous charging and discharging, impressive reliability, and extended lifetimes.
Active Voltage Correction with Batteries
Alternatively,
AVC with batteries can be equally effective. Performing the same function as ultracapacitors, a battery-operated system will come with lower up-front capital requirements countered by more regular maintenance for your batteries. While this maintenance is less taxing than alternative methods, batteries typically require replacement every seven to ten years in order to keep your system running at full capacity.
Long Runtime Solutions
If you are interested in investing in a power outage prevention system with a longer runtime, the best option is a generator system with an automatic transfer switch. These generators provide constant voltage sterilization via regulation for complete control of your power supply. Available in diesel or natural-gas powered choices, they are the ideal long-term runtime power supply solution for most facilities.
By coordinating and properly sizing your
voltage regulator, battery system, and emergency backup generator, your entire system will be poised to work efficiently and quickly during an outage event. Similarly for data center’s, systems such as
Eaton UPS Systems may be used for Industrial UPS Applications.
Have an ICP Site Survey Conducted
When you install power correcting equipment, you are providing your facility with protection against all outside influences on power supply. Having that stable voltage and power reduces wear and tear on your facility as well, adding up to a wide array of long-term benefits and lowered operation costs.
Voltage Correction is here to help review your power consumption and issues in order to increase efficiency in your facility and correct facility power issues with real solutions. If you’re ready for a product solution, metering, or want to request a site visit,
contact our team today and let us know how we can help. Call 855-240-6776
Connect with Us:
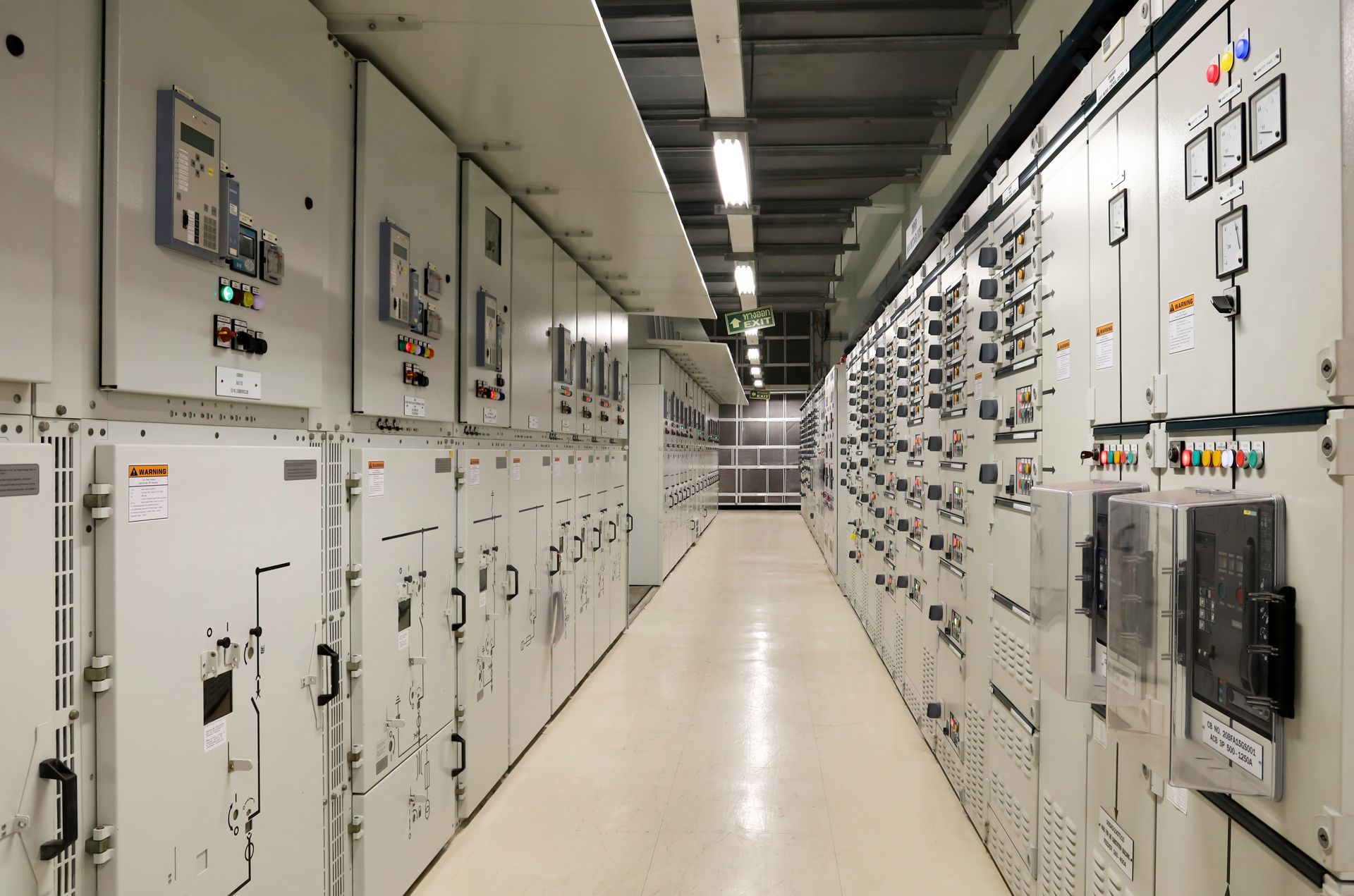
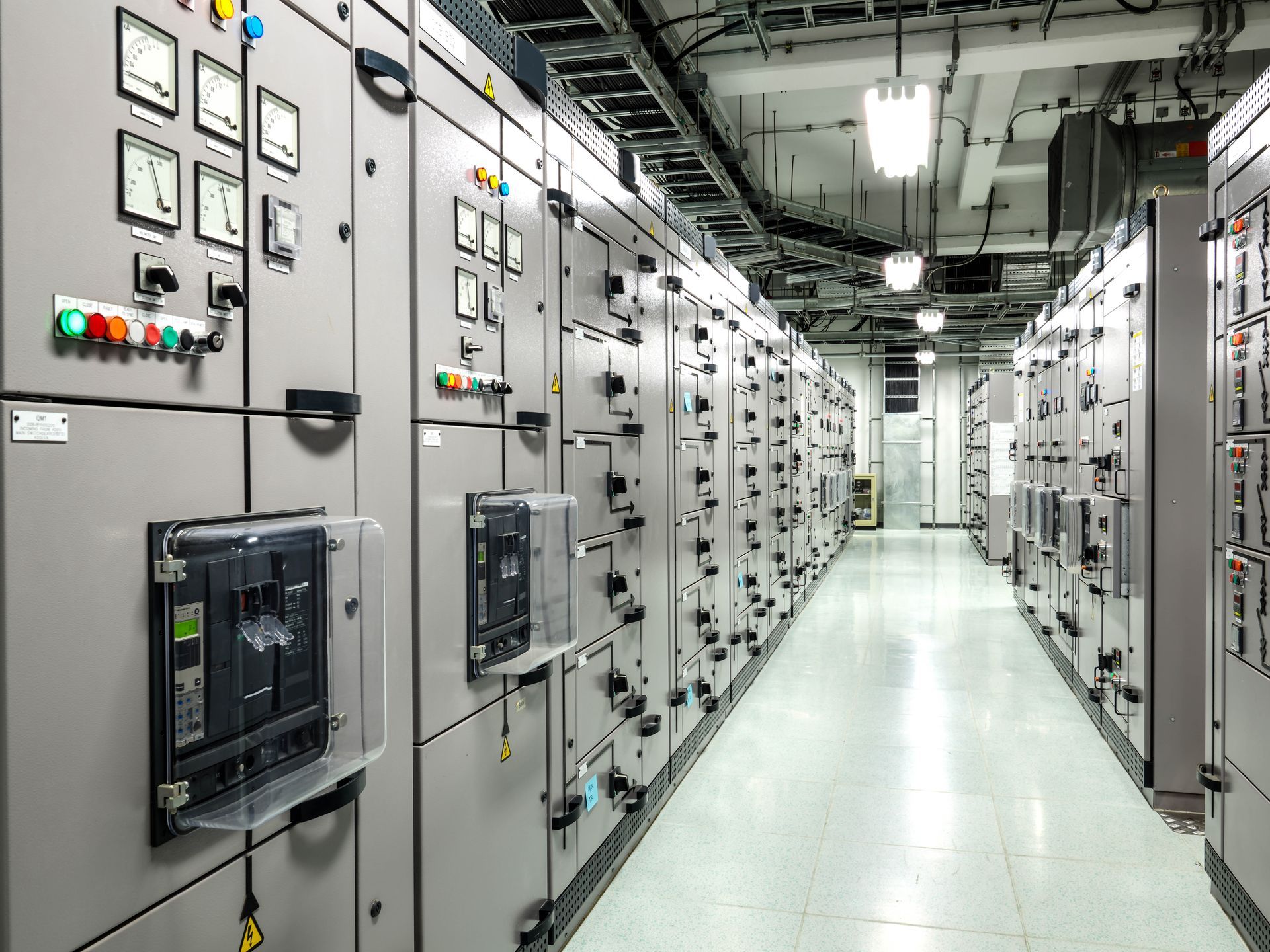